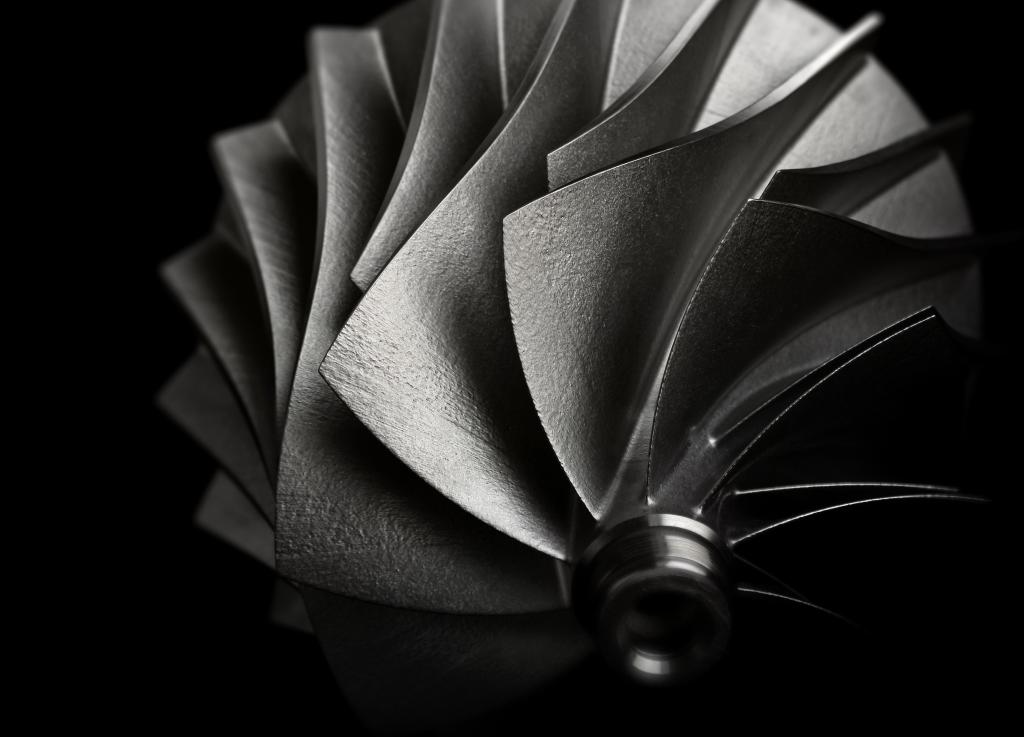
Beehive, ORNL Propel Aerospace 3D Printing Advances
Beehive Industries leverages cutting-edge additive manufacturing to create precision components for jet engines in collaboration with ORNL’s Manufacturing Demonstration Facility. Credit: Beehive Industries
When Jonaaron Jones started his master’s degree at the University of Tennessee, Knoxville, his mentor invited him to visit the Manufacturing Demonstration Facility, or MDF, at Oak Ridge National Laboratory. “I saw a metal 3D-printed part for the first time,” said Jones. “I knew I was seeing the future – for industry and for me.”
Over the next few years, Jones worked in the MDF alongside advanced manufacturing experts from UT and ORNL. His experiences there launched him on a cutting-edge career path in additive manufacturing for aviation, defense and energy applications, first as founder of start-up Volunteer Aerospace and now as part of Beehive Industries , a U.S.-based additive manufacturing company that specializes in the design and development of jet engines for defense applications as well as parts manufacturing. With Jones as president and general manager of its external parts business, Beehive continues to demonstrate what it means to partner with the MDF to drive technical and economic growth for the United States.
Volunteers in action
As Jones’s mentor, Suresh Babu, former UT-ORNL Governor’s Chair of Advanced Manufacturing, connected him to MDF experts and resources, as well as partners within the aerospace, defense and energy industries.
In 2015, Babu led UT and MDF researchers in a project with industry partner Aerojet Rocketdyne that was supported by the Air Force Research Laboratory and the Defense Production Act under the federal Title III cost-share program. Jones and other team members sought additive manufacturing solutions to aerospace supply chain challenges, including long lead times and quality issues for cast parts.
Specifically, they set out to 3D print aluminum parts for the RL10 liquid rocket engine manufactured by Aerojet Rocketdyne. Aluminum for additive manufacturing was still very low in technology readiness at that time, and they faced challenges from the start due to a lack of material and machine options.
“We essentially had to apply aluminum powder atomized for other applications, like automotive,” Jones said. “We learned that powder requirements were different. For example, we had to correct for moisture content.”
The team also had to find a machine big enough to produce rocket parts. At that time, the largest on the market was Concept Laser’s X-Line 1000, intended for prototyping small automotive engine blocks. The team set up one of these machines in the MDF.
“The rocket parts at least fit inside, but it wasn’t designed for the level of quality we needed,” Jones said. “I volunteered to take on making the machine usable for our project. I realized I had all the people and resources I needed at my fingertips. I worked with different groups around the lab to identify problems, solve them at the basic science level, apply the fixes and test them. A company doing this on its own wouldn’t have had that advantage. After we worked on the machine and the material feedstock, the difference was night and day.”
At the end of the program, Aerojet Rocketdyne decided not to relocate this printer to its production facilities. Title III requirements, however, meant the equipment must be used to develop the defense supply chain.
Jones and two soon-to-be business partners – his wife Rachel Cade Jones and ORNL colleague Devon Burkle – envisioned a solution. In 2016, they sought approval from all entities involved in the project to start their own business, Volunteer Aerospace.
In 2017, they moved the X-Line 1000 printer out of the MDF into a facility 10 minutes away. Volunteer Aerospace soon added new employees, machines and clients including Boeing, Lockheed Martin and Northrop Grumman.
“We became the industry leader in large aluminum parts,” Jones said. They also supported the MDF on material development and other ORNL teams on small yet complex projects, such as printing a distillation column for carbon capture.
Volunteer Aerospace caught the attention of Beehive Industries. Beehive acquired Volunteer Aerospace in 2021 to support its vision of powering American defense by scaling its core capabilities, employee base and resources.
https://www.ornl.gov/news/how-beehive-industries-ornl-are-advancing-aerospace-additive-manufacturing